Bella™ Dryer/Cooler
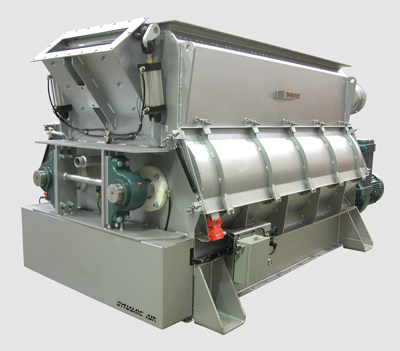
The Perfect Way to Heat, Dry, Cool or Moisturize Dry Solids
The Bella™ dryer/cooler offers a highly efficient method of drying or cooling powders, granulates and filter cakes. The super fast mixing capability of the Bella dryer/cooler makes it an ideal heater or cooler, since the process of drying or cooling is simply the mixing of heated or cooled air with any given material. The better the mixer, the better the dryer.
Since the Bella mixer is one of the fastest mixers for mixing dry granular powders and granulates, when used as a dryer or cooler it becomes highly efficient and creates some very high energy savings which can have a huge impact to lower operational costs.
In addition, the gentle agitation of the mixing paddles produces a very desirable finished material which is consistent in texture, moisture and particle size.
With the twin counter rotating paddles, dead zones are eliminated because each and every particle being dried or cooled is in constant motion and moving in numerous random directions. Material is never allowed to stagnate, thus increasing its total exposure time to the heated or cooled air to improve performance and efficiency. Thus, the heated or cooled air is allowed to easily move in and around each particle because the material is slightly suspended as a result of the constant agitation of the paddles as it moves the material in and out of the weightless zone before the heated or cooled air is allowed to exit. This process also maximizes the total surface of the material which is exposed to the heated or cooled air, thus increasing the thermal efficiency. The drying process will naturally go through an adiabatic evaporation with thermal efficiency as high as 80 percent. Therefore, smaller air volumes are required.
How it works

Figure 1
The Bella dryer/cooler consists of twin drums which have two counter rotating agitators with specifically angled paddles. The paddles sweep the entire bottom of both drums. The material moves in a horizontal counterclockwise direction at the perimeter while simultaneously moving both left and right in the center (figure 1). The heated or cooled air enters all along from the top of the Bella dryer/cooler at Zone B and Zone C. The air then moves downward in the direction of the moving agitators (figure 2), moving in and around the material and in and out of the of the weightless zone.

Figure 2
The material in Zone B and Zone C (figure 2) is in its normal gravimetric state as material and air is being moved and directed by the agitators. In Zone A, a fluidization or weightless zone is created that effectively lifts the material to an almost weightless state allowing the material to move freely and randomly and mix thoroughly with the heated or cooled air. Thus the heated or cooled air achieves maximum contact with the material for maximum efficiency
Heating/drying/cooling procedure
The supply air inlet temperature can be as high or as low as the product will allow to keep the drying or cooling time to a minimum. Once the drying/cooling process has begun, the product temperature immediately rises or falls to a predetermined maximum allowable reading.
The exhaust air temperature will be only slightly higher or lower than the product temperature and is a measure of the dryer’s efficiency. The closer the relationship between the exhaust air and the product temperature, the higher the thermal efficiency of the process.
Drying/cooling is dependent on four parameters: air/gas flow, temperature, relative humidity and efficiency. The Bella dryer/cooler optimizes these parameters and product moisture quickly reaches the desired level.
Benefits
- Improved material characteristics
- Excellent heat transfer rates
- High thermal efficiencies
- Added mixing capability
- No material stagnation
- Minimal exposure time
- Operating temperatures from
- -150° F (-101° C) to +900° F (482° C)
- Gentle, low shear agitation
- Easy access doors
- Low maintenance requirements
- Low energy requirements
- Continuous or batch operation
Applications
- Weigh reduction
- Volume reduction
- Reclamation
- Liquid/solid separation
- Dewatering
- Foundry shakeout sand cooling/drying
- Product sterilization
- Crystallizing PET
- Organic and inorganic compound drying
- Detergent powder drying
- Milk powder drying
- And many more
Download PDF
Request a Quote
Let’s Find the Right Solution for You
Contact usPartner with Dynamic Air, the industry leader in providing reliable, innovative solutions. Our team of experts is ready to understand your unique requirements and design customized solutions tailored to your specific needs, whether it’s pneumatic conveying, equipment manufacturing, or other material handling challenges. Experience the Dynamic Air difference and unlock the potential of seamless material flow, enhanced efficiency, and optimized productivity. Contact us today to discuss your project.